Business Management Programs For Machine Maintenance
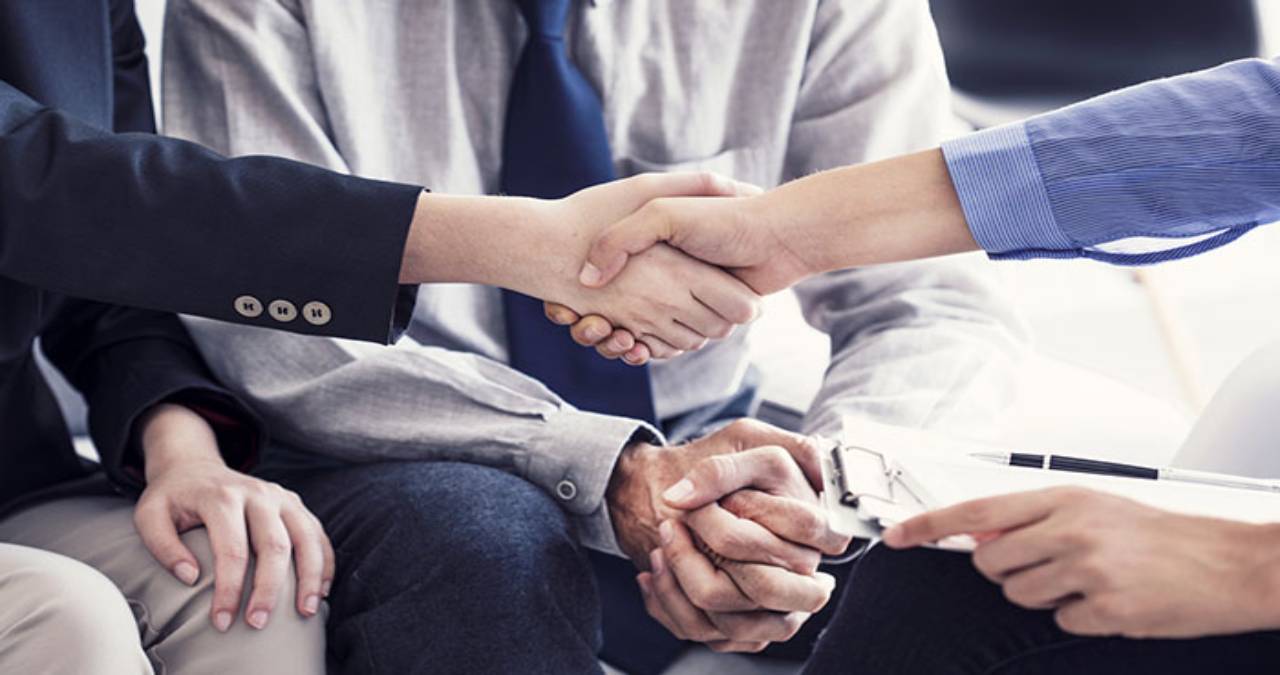
Business management programs have many benefits. One of the most important processes of companies dedicated to the production of goods, especially industrial ones, is the correct maintenance of their machinery. If the appropriate precautions are not taken, the machines can suffer considerable damage and their consequences can be catastrophic for the viability of the company.
Thus, the reliability of production plants depends to a large extent on proper maintenance. A process for which it is important to have a management program that helps and incorporates all the relevant information to carry it out properly.
Table of Contents
Corrective Maintenance And Preventive Maintenance
Before talking to you about the role of business management programs in maintenance management, it is necessary to make clear the two formulas for proper maintenance of the machines of a company that is dedicated to production: corrective and preventive.
Corrective maintenance is one that takes place at the time when an error or machine failure occurs. Normally, it consists of changing broken parts or repairing hydraulic or electrical problems.
The preventive maintenance, however, and as the name suggests, is conducting periodic reviews aimed at ensuring the proper functioning of infrastructure and the machines analyzed. In this, a series of actions are carried out to preserve the system . Normally, it is enough to check that everything is fine, for which a routine inspection is enough. In general, preventive maintenance should be sufficient to avoid possible machine failures.
Most companies can not afford these to suffer any error or breakdown that means stopping production. That is why preventive maintenance is so important that it saves money since it minimizes the problems related to possible machine failures.
The Importance Of Preventive Maintenance At An Industrial Level
Both types of maintenance are essential and complement each other perfectly to ensure proper factory operation. However, the reality is that the preventive procure greater cost savings, since it avoids, among many other setbacks, the following:
- The cost of repairing the machines. This includes, in addition to many others, the cost of subcontracted materials, personnel, or services.
- Other more serious faults, that have a more difficult solution and that can appear as a consequence of a chain reaction that damages the machines or the facilities.
- Possible losses in production, which are not only limited to the amount of product that is discontinued but, above all, to the disruption that occurs in everything that has to do with the planning of deliveries and customer service.
- Possible risks affecting workers. Some faults can cause accidents that, depending on the type of fault, can be very serious.
How Business Management Programs Help To Maintain Well
In an environment in which change is constant, industrial companies also have to adopt the necessary tools to catch up on both productivity and cost savings.
Advantages Of Business Management Programs For Maintenance
Performing maintenance using business management programs has several advantages for organizations:
- Free maintenance personnel from the simplest, most routine tasks with the least added value. Thus, employees can engage in those activities that are really of interest to the company.
- Motivate operators, since their work is focused on making the system work and that it works as efficiently as possible.
- Save costs. On the one hand, because not so many people are needed to carry out this type of task and, on the other, because it reduces errors caused by poor system maintenance.
- Reduce downtime, as these operators are capable of solving everyday breakdowns.
Disadvantages Of Business Management Programs For Maintenance
Business management programs are very useful for all industrial companies, but the truth is that some drawbacks need to be known, although, in reality, they all have to do with change:
- The knowledge of operators at a technical level has to be higher. They need to know how to use the software and understand what is required of them.
- Implementing a maintenance management program involves a profound change in procedures and, above all, a mentality, which is not always easy to start or achieve.
How To Implement A Business Management System For Maintenance
Business management applications and programs are typically rolled out progressively. Sufficient implementation time is required and many of the current procedures need to be corrected and adapted. Deployments from scratch are very risky because all the problems and unforeseen occur at the same time and a lot of discomforts are generated.
Therefore, the most reasonable way to implement a business management program for maintenance is to gradually replace or improve those procedures that avoid the most serious corrective actions or anomalies due to security, costs, or dedicated resources. In this way, the results are visible from the first day, which serves to save costs and identify flaws in other procedures.
Also, and since the system is built on the fly, the corrections applied to the first procedures are taken into account to create the following ones, which saves many modifications. The last link in this chain should serve to correct the simplest errors so that the program is applied in all the company’s processes.
As you can see, business management programs can be very useful for machinery maintenance in your company, especially if it is an industrial company.