Collaborative Robotics How Do Robots Help Humans In Industrial Work
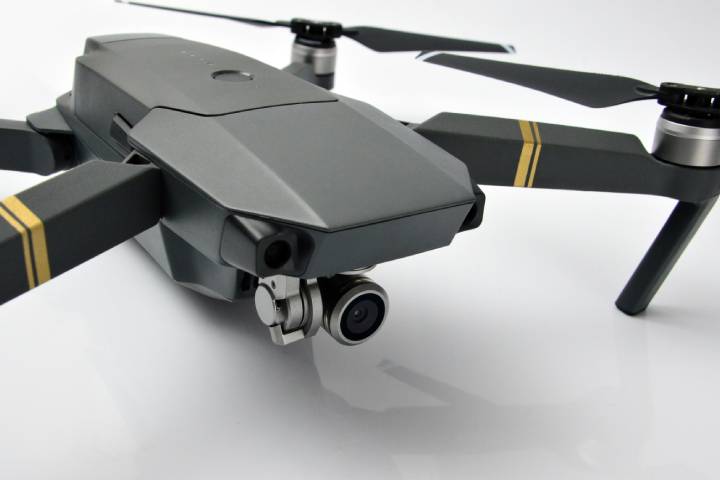
Robots are key tools in improving worker productivity and performance in today’s industrial companies. Although many sectors have been working with robots for decades, the latest advances in collaborative robotics allow their implementation in a more significant number of factories. Since the appearance of the first robots, society has wondered if machines would replace humans at work. Now that collaborative robotics is a reality in industries, the coexistence between workers and machines seems more transparent and positive.
In recent years, the market for collaborative robots, or cobots, has boomed in the industrial arena. These types of machines are designed to support human labor in industrial companies. That is to say, they do not imply the total automation of work but rather coexist with the workers to improve production methods.
Unlike traditional industrial robots, collaborative robotics is characterized by the ability to detect the presence of people and interact with them, too, among other things, to prevent accidents. These machines are more compact and lighter than conventional robots. They can be easily moved around the factory and are capable of performing different functions within the production chain itself.
With a lower cost, all these characteristics make collaborative robotics a more accessible option for SMEs than conventional robots. It will be possible to automate production in a more significant percentage of the industrial fabric thanks to it.
Table of Contents
Collaborative Robotics And Smart Factories
The concept of industry 4.0 (or the fourth industrial revolution) would not be understood without the existence of Smart Factories. These intelligent factories are highly automated and digitized and use collaborative robotics to create a more efficient and fluid work environment.
Smart Factories put people at the center of their activity. Thanks to collaborative robotics, workers can focus on performing work that requires human capabilities. They are freed from routine, heavy or dangerous tasks, and optimized processes.
The most common collaborative robots are in charge of the “pick and place” function, that is, the task of picking up an object and placing it in another place. We can also find them in assembly lines or in the warehouses of intelligent factories, where they are capable of repeating the same movement with perfect precision.
Collaborative robotics reduces the health risks derived from tasks that require the use of force, forced postures, or the handling of dangerous substances. Furthermore, cobots are designed to ensure the safety of workers when interacting with them. Some of the most common uses of robots in factories are painting, welding or packaging, and handling pallets.
Also Read: Robotics – How Robots Will Help In Education
Safety Is A Priority For Collaborative Robots
Collaborative robots have several features that improve safety in Smart Factories. For example, they have low-inertia servo motors or elastic actuators, which offer a very reliable response and are made of light materials and rounded contours. The defining aspect of collaborative robotics is sensors that ensure safe interaction with people. According to the international standard ISO 10218, we find four types of robots according to their safety functions:
1. Safety Guarded Stop
These cobots typically work independently, performing a primary task, while the worker performs a secondary role. However, sometimes employees need to interact with the machine. When a human approaches a certain distance, this robot completely stops its activity. The safety monitored stop function is implemented in conventional robots utilizing special sensors.
2. Speed And Separation Monitoring
In this case, the robot monitors its surroundings and can detect the proximity of workers. Unlike the first type, it progressively reduces its speed depending on the workers’ distance. If it gets too close, it can completely stop its activity. This feature of collaborative robotics is used in jobs that require the frequent presence of people.
3. Hand Guide
This type of robot can learn trajectories with the help of a person. This is a valuable function for quickly programming a new guideline, for example, for a pick and place machine. They are conventional robots equipped with a sensor like the two previous types.
4. Limitation Of Force And Energy
It is the most common and safest type of collaborative robot. At the same time, the former use standard industrial robots with additional sensors, these types of machines are specifically designed for interaction with people.
These cobots have all kinds of sensors that allow them to detect abnormal forces in their activity. This allows them to respond immediately when they contact a human. In this way, they can stop to avoid injury or dissipate some of the energy of the impact. In addition to being very light, these robots sometimes have an outer shell that absorbs shock.
Advantages Of Using Robots In Smart Factories
We have seen how safety is the main feature distinguishing collaborative robotics from traditional industrial robots, and its application can reduce and avoid risks and injuries characteristic of factories. In conclusion, collaborative robotics is a key tool for security understood as ” safety, “that is, the protection of employees.