How Do We Measure Overall Equipment Effectiveness?
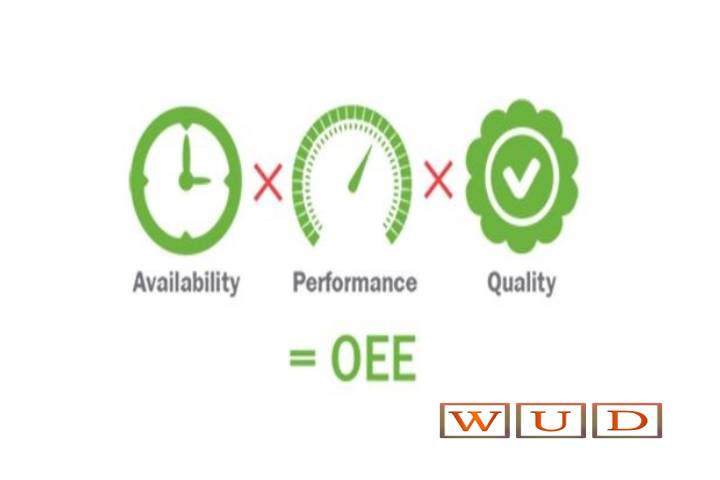
The time when limited businesses aimed for a global reach is long gone. The modern market is inundated with organizations looking to garner a worldwide audience. As more advents and practices are being invented, spreading a global reach is becoming routine. This has led to a shrewd increase in the competition, and the sole way to keep up with the market standards is to equip the latest tech and business practices.
Such practices and technologies can help you assess your business productivity and efficiency to formulate their strategies. There are numerous examples of handy tools and exercises that businesses can avail of to serve the purpose. However, even amidst the long list of available alternatives, OEE or Overall Equipment Effectiveness emerges as the best possible option.
Equipment management is pivotal for a firm’s effective functioning, and “Overall Equipment Effectiveness” is the ideal way to ensure that. OEE makes sure that your assets are not merely functioning, they are in mint shape as well. This minimizes machine downtime and helps the organization operate in its optimal state.
Since OEE holds great significance in the modern market, every rational firm invests some time to learn how to calculate it. If you are also trying to learn the same one of the businesses, read through and find the simplest way to calculate Overall Equipment Effectiveness:
Table of Contents
What is OEE/Overall Equipment Effectiveness?
OEE, also known as Overall Equipment Effectiveness, is the ideal standard for calculating manufacturing productivity. In simpler terms, the method calculates how much of the manufacturing period is actually productive. OEE is calculated in percentage, and a different percentage shows different productivity standards.
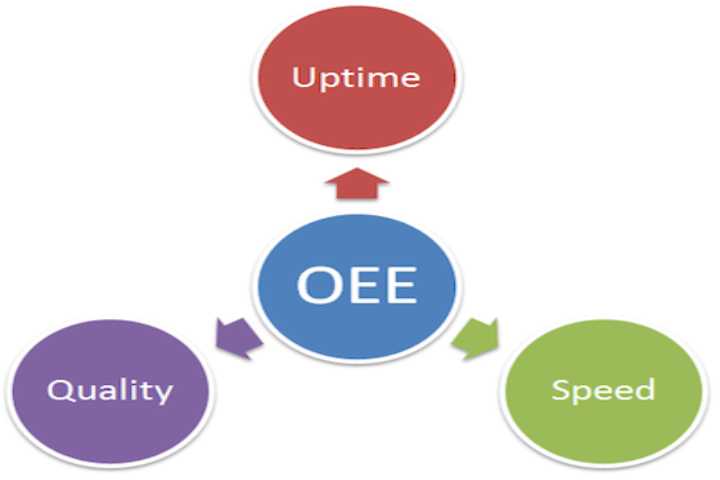
OEE is not merely used to measure productivity but can also be used to carry out maintenance and formulate provisional strategies. The term predictive maintenance definition is popular on the web, and rightfully so since OEE can be used to conduct predictive maintenance in your organization.
OEE Benchmarks to Understand Production Quality
Here is how OEE can help you assess your manufacturing productivity:
- Scoring an OEE of 100% is considered perfect, as it means your organization is indulging in the best possible production module. You are not facing any downtime, and the production is done ideally.
- If you are scoring an OEE of 85%, your business is reaching its long-term goals. The results are top-class, and only a minority of the organizations can maintain such a percentage.
- In case your OEE score is 60%, you have vast room for improvement.
- An OEE score of approx. 40% is not uncommon but it is not desirable either. It indicates that your business is lacking on several fronts and is in dire need of improvement.
Now that you know what the Overall Equipment Effectiveness score is and how it represents your production quality, it is time to learn how to calculate OEE.
Also Read: Most Of The SMEs Rely On Artificial Intelligence To Gain Visibility
How To Calculate OEE Or Overall Equipment Effectiveness
Calculating OEE opens the door for systematically impairing your manufacturing procedure, so it makes sense for every organization to indulge in the practice. However, before learning how to calculate it, you should first learn what efficiency and effectiveness mean in the context of OEE.
When it comes to OEE, effectiveness can be defined as the correlation between what can be produced and what is produced in a specific production span. For instance, in case your machinery can produce 100 products every hour but are producing only 75, they are 75% effective.
Although it is a good indicator of your productivity, it does not represent your efficiency. Since, the practice does not account for factors like energy, materials, and operators required to reach 75% effectiveness. For instance, assume your machine is 60% effective with one labor and is 75% effective with two laborers. Under such circumstances, your overall effectiveness rises by 25%; however, your efficiency reduces to 50% on the basis of labor.
Now that the difference has been established, let’s learn how OEE can be calculated. Here are the two ways to calculate Overall Equipment Effectiveness:
- Simple Calculation
- Preferred Calculation
Simple Calculation
It is the simplest and most commonly used way to evaluate Overall Equipment Effectiveness. In this method, the overall production time is divided by the total planned production time. Its formula looks like this:
Overall Equipment Effectiveness = Best Cycle Time x Good Count / Total Planned Production Span
Preferred Calculation
The aforementioned three factors play a part in this process as well – performance, quality, and availability. This way, the formula looks like this:
Overall Equipment Effectiveness = Performance x Quality x Performance
The method is termed preferred since it shows you the OEE score alongside the three factors showcasing the reasons behind your losses.
To put things into a better perspective, let’s look at an oee calculation example.
Here are some random stats the example would be using:
- Downtime – 4%
- Efficiency – 95%
- Quality – 98%
Now suppose a machine with 4% downtime or 96% availability possesses a 95% efficiency. Out of every 100 machines, 2 are rejected, leading to 98% quality. Under the circumstance, the OEE score would 0.96 x 0.95 x 0.98 (Availability x Performance x Quality) = 89.38%
To clear up the theatrics, let’s glance at another example. The standard shift at a packaging facility accumulates to 540 minutes. The operators take 3 breaks in their shift totalling 50 minutes, and they also indulge in 2 changeovers leading to 60 minutes per machine downtime (180 minutes total).
- The availability, in this case, will be:
540 minutes – 180 minutes = 360 minutes
360 minutes / 540 minutes = 66.67% availability
On to the performance section, assume the factory produces 60 packages per minute. As per the 360 minutes availability, the packaging would account for 21,600. Assume the machinery is operating 2 seconds slower, reducing the speed by 1/2. This would lead the production performance to 10,800.
- Now the performance would be calculated as:
2 seconds per bottle = 50% performance
For the quality section, assume out of 10,800 packages, 1,800 does not match the quality standards.
- Now the quality would be calculated as:
10,800 – 1,800/ 10,800 = 83.34% quality
Now to calculate the OEE score, you have to multiply the Availability x Performance x Quality. In this case, the calculation will go like 66.67% x 50% x 83.34% = 27.78% OEE. This means the firm can produce approx. 38,572 packages but is only producing 10,800. (10,800 / 38,572 = 28% approx.)
Wrapping Up
Overall Equipment Effectiveness is one of the most effective production measurement methods on the web. Nowadays, every business worth its salt is using the practice to enhance its routine proceedings and expand its reach. However, there are still numerous firms that do not know how to calculate OEE.
The blog has presented a simple definition of OEE alongside a straightforward way to calculate OEE. There are also some examples to clarify the process to calculate OEE, so read through and easily calculate your venture’s OEE score.
Also Read: Cybersecurity In The Times Of Edge Computing