The Six Sigma Methodology – How Does It Works?
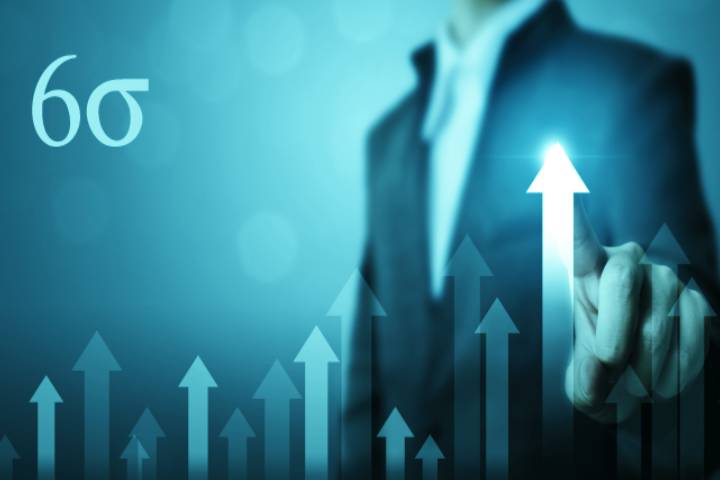
Companies must adapt to a constantly changing world and focus their efforts on achieving maximum efficiency. We are linearly used to thinking and sometimes underestimate the speed and scope of progress underway. For this reason, the degree of need for change is high, and companies need to detect obstacles to change in time, identify priorities, create new ecosystems, perfect the business architecture and create a plan (where everything always revolves around customers).
This is the objective of Six Sigma, to provide a methodology that responds to organizational needs. It is an improvement strategy whose aim is to detect and eliminate the causes responsible for the failures or defects in the processes that affect the critical characteristics of the products or services that are of vital importance for the clients. Its engine is the powerful DMAIC improvement cycle: Define, Measure, Analyze, Improve, and Control.
From a functional point of view, Six Sigma is based on analyzing empirical data and statistical tools to reduce the risk of error in production processes, something fundamental to measure a company’s operational efficiency. Six Sigma is a disciplined, structured, and quantitative management system that increases customer satisfaction, reduces costs and optimizes manufacturing processes. A management system that goes hand in hand has many meeting points with Lean Management, where continuous improvement from workgroups solves problems and drives value flows.
Table of Contents
But How Does Six Sigma Work?
In statistics, the Greek letter “Sigma” (Σ, σ, or ς, depending on its location within a word) represents the deviation from an expected result. There are different levels of Sigma in production processes, depending on the number of defective products per million units delivered to the end customer (DPMO). The objective of the Six Sigma methodology is to improve the procedures of the company until reaching a Sigma 6 (3.4 DPMO). This implies a degree of efficiency greater than 99%. Hence, the “Sigma” concept is associated with efficiency.
Six Sigma Techniques: DMAIC And DMADV
The Six Sigma methodology is usually used to improve processes or products that already exist in the company. It is based on the DMAIC method (Define, Measure, Analysis, Improve, Control), which consists of 5 phases:
Define (Define)
It consists of finding the problem, defining it in detail (which areas it affects, what processes are involved, who could be in charge of improving these processes, etc.), and validating it.
Measure
In this second phase, all the activities carried out during the erroneous process are recorded to understand the operation of the problem (studying variables such as customers, product characteristics, etc.) and check if the company can find a solution.
Analyze
The objective of this phase is to analyze the natural causes that have caused the problem or defect. Data and figures related to the processes that are to be optimized to find cause-effect relationships are studied.
Improve
The extracted cause-effect relationships make it possible to determine what improvements are necessary and optimize each phase of production. It is required to test various options to find the optimal solution.
Control (Control)
It’s about preventing the same mistakes from being made again. This last phase of the Six Sigma method includes taking the necessary measures to guarantee the continuity of the improvements implemented.
Apply the DMADV method
When Six Sigma is applied to processes or products that do not yet exist, they have based on the DMADV (Define, Measure, Analysis, Design, Verify) method, which differs slightly from the previous one. Its phases, in this case, are:
Define (Define)
It consists of defining the process that we want to implement.
Measure
That is, calculate how the process will develop according to all possible variables.
Analyze
It is about establishing criteria to measure and design the new process, analyzing each phase, verifying if they add value, and locating possible errors to find preventive solutions.
Design
Thanks to the previous analysis, it is possible to establish the parameters that help us design a production model according to our needs and objectives.
Verify
To verify the design, it is necessary to analyze each phase, paying attention to the metrics and the established parameters.
What Advantages Does Six Sigma Offer
The main advantage of Six Sigma as a methodology for the quality control of processes and products is that it is oriented to the end customer. In addition, it is a proactive method because it establishes how to make improvements even before defects in the processes are detected. This is especially important for small companies and SMEs, making quality a differentiator against their competition. The Six Sigma methodology also seeks profitability and the highest return on investments. This aspect is reinforced because it involves all the professionals and areas of the company, obtaining global results.
Finally, Six Sigma is compatible with the Lean methodology, a working method that, having the appropriate indicators, helps to achieve business success. The success that works with the organization’s people helps to optimize efficiency through the simplification and automation of production. There is a hybrid methodology called Lean Six Sigma and based on the constant improvement of the company’s production processes in a simple way.
These methodologies, together with a culture change, can be decisive elements in an organization. And it is that Peter Drucker said that culture has breakfast for strategy. The management team drives change, goes from me to us, from control to trust, from guidelines to responsibility, from avoiding mistakes to trying and learning, and transformation comes.
Also Read: Different Approaches To Managed Services In The Placement Market